The new market sensation
LEIFELD WSC Flex
The flow forming technology has been embraced across the globe: The LEIFELD WSC Flex goes one step further and revolutionizes the market. The new machine for manufacturing rims is using a flow forming process, which, for the first time ever, works with inner rollers.
No tooling is needed, no time-consuming changeovers. The LEIFELD WSC Flex increases efficiency by a minimum of 15% and gives manufatures maximum flexibility in production and wheel design. What makes it a real game changer: batch size one can be produced economically.
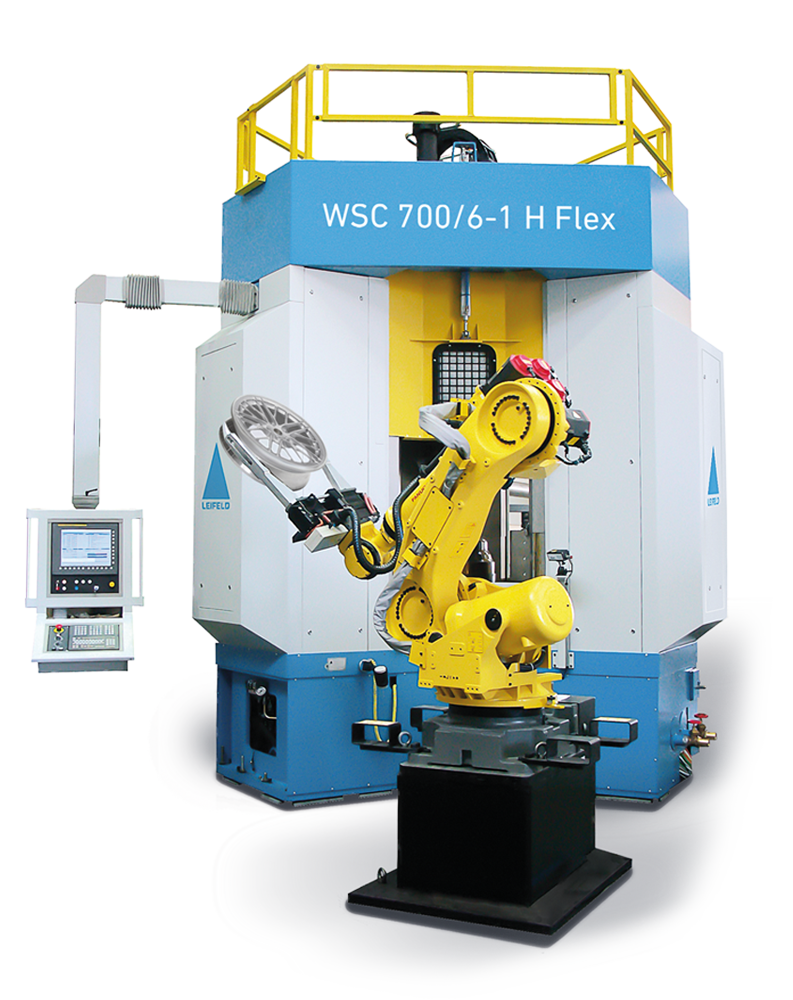
15 %
more efficiency
10 %
energy savings
No tooling
needed
Batch size one
produced economically
Top features
no tooling
no changeover
independently controllable inner and outer rollers
multi-functional clamping chuck
Top benefits
economic production of batch size one
Maximum flexibility in wheel design
Increased efficiency and reduced costs
Energy savings
Lean manufacturing possible
Wheel Manufacturing Reaches a New Level
Learn more about "WSC Flex Technology"
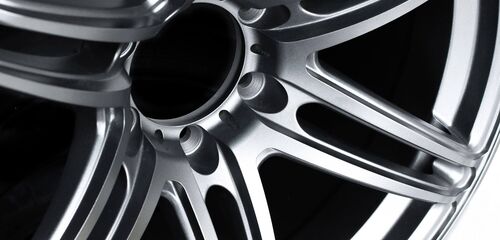
Growing design complexity and increasing wheel size along with increasing variant variety and rising cost pressures are just some of the trends that are currently shaping the wheel market. Manufacturers have to be able to react very flexibly to these market developments in order to keep up with demand and competition.
Current market trends and outlook
Visible trend towards larger sized wheels | |
Increasing number of different wheel variants | |
Decreasing production batches based on just-in-time production | |
Legal requirements to reduce CO2 emissions require weight-reduction for wheels | |
Market share of flow formed wheels is increasing, inter alia through rising importance of electromobility | |
Wheel manufacturers who have not used the flow forming technology so far are planning to use it | |
Increasing interest in flow forming machines on the after-market |
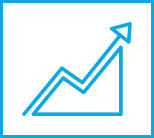
The results
The need to produce wheels by flow forming technology is now greater than ever. Due to higher price competition, incentives to minimize production costs and generate USP’s are more important than ever before.
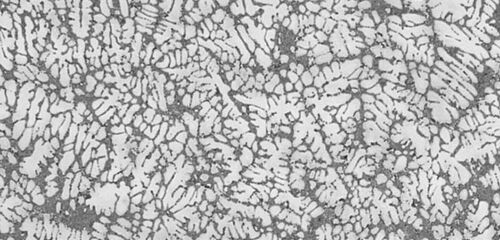
Aluminum rims are often cast or forged as single pieces. The flow forming process improves the material’s grain structure, which significantly increases the final rim strength after heat treatment.
Improved microstructure and increased strength
increased strength enables additional reduction of the material cross-section or the use of more cost-effective material | |
wall thicknesses in the cross-section can be adapted to the load request of the wheel resulting in flexible wheel design | |
optimal weight savings for the wheel |
Cost and Material Savings
Reduction of scrap wheel preforms | |
Reduction of recycled material | |
Reduction of the allowance for turning operation | |
Reduction of wall thicknesses for the final part caused by optimized material properties after heat treatment |
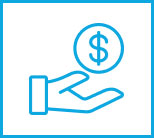
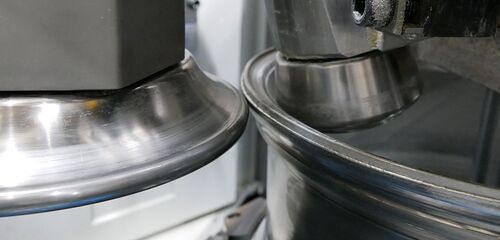
We offer the LEIFELD WSC Flex with various workpiece changeover concepts and with different numbers of rollers, depending on customer-specific performance requirements. The cycle times of the new machine are comparable to those of tool-bound machines. One function that was previously not available allows a completely cylindrical region to be formed with the new process for improved wheel stability.
The new process also offers numerous advantages for manufacturing of forged aluminium wheels. With the new WSC Flex Technology, the user has the option to chaotically produce 18- to 24-inch wheels starting at batch size one.
Forming principle similar to pottery
The human brain of a potter is being replaced by CNC Control. | |
The inner hand is being replaced by the inner roller. | |
The outer hand is being replaced by the outer roller. | |
The clay is being replaced by alu. |
Our patented LEIFELD WSC Flex Technology works flexibly without tools. The principle resembles throwing pottery. The forming movement of the hands is similar to the axial and radial movements of the inner and outer rollers.
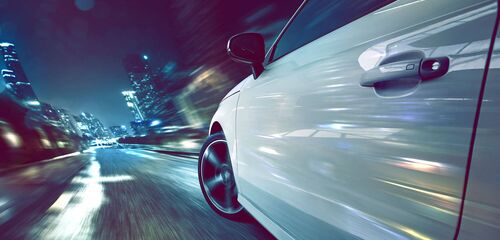
For manufacturers of aluminum wheels, our patented WSC Flex Technology is a real sensation. It offers far-reaching potential in wheel manufacturing for improving productivity, lowering cost, and thus creating relevant competitive advantages for OEMs and after sales wheel manufacturers.
Machine features:
No tooling and no changeover of tools | |
No gas burner is required as preheating the tool after a product change is no longer necessary | |
Independently controllable inner and outer rollers with automatically adjustable axial and radial offset | |
Inner roller with automatic angle adjustment | |
Emulsion is used for roller spraying | |
Multi-functional clamping chuck for flexible workpiece holding | |
Three access areas - two areas for part changes and one for process observation | |
Synchronization via CNC control | |
Offline programming via FlowSpin Software |
Your benefits:
Efficiency increase by a minimum of 15 percent | |
Working with High-Mix Low-Volume Manufacturing (HMLV) lot size one can be produced economically | |
10 % energy saving by reducing the preform temperature | |
Maximum flexibility in wheel design thanks to new machine functions:
|
|
Increased material strength allows more flexible wheel design and maximum weight savings | |
No product-specific tooling costs in terms of production, storage, maintenance | |
No set-up times:
|

LEIFELD WSC 700-6-1 Flex
Outside diameter min. | 410 mm |
Outside diameter max. | 720 mm |
Nominal rim diameter min. | 18 inch |
Nominal rim diameter max. | 24 inch |
Rim width min. | 3 inch |
Rim width max. | 14 inch |
Workpiece length approx. max. | 400 mm |
Work piece mass | 18-40 kg |
Full machine data, information about machine configuration and prices on request.
our innovative process
Highest Flexibility Without Tools
There are more than 130 LEIFELD machines for wheel manufacturing in the field, smoothly running in full time production over years. Which highlights the high quality and longevity of our machines. To support our customers even better in reacting to market trends such as increasing wheel size and variety or just-in-time production with a high level of flexibility, we revolutionized the well-known flow forming process. The result: The patented LEIFELD WSC Flex Technology that works flexibly without tools.
Our innovative process enables users to be as flexible as it gets and produce different rim diameters, profiles, wall thicknesses, and rim widths. Whereas classic flow forming uses one tool per rim type, the new LEIFELD WSC Flex uses no tools whatsoever and comes with a multi-functional clamping chuck. That means: No setup times and no product-specific tooling costs during operation. Tooling procurement costs, storage, and repair are eliminated completely. As a result, production factors are used economically and efficiently, so lean production can be realized. The user can carry out product changes seamlessly without having to perform disruptive setup activities.
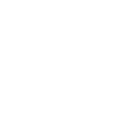
Worldwide unique patented technology for chaotic production of cast aluminum wheels makes automatic product changeover possible in seconds.
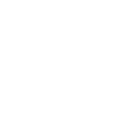
Wheel designs with undercuts that were not possible on a conventional mold previously are now enabled by the inner roller technology.
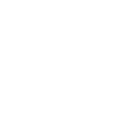
Significant CO2 reduction through state-of-the-art energy-saving measures such as recuperation on the main drives.
Market leading developments by Leifeld
6.125+ sold machines Worldwide
Are you ready for the next step?
Get in touch with us
Book a free expert call and learn more about WSC Flex Technology.